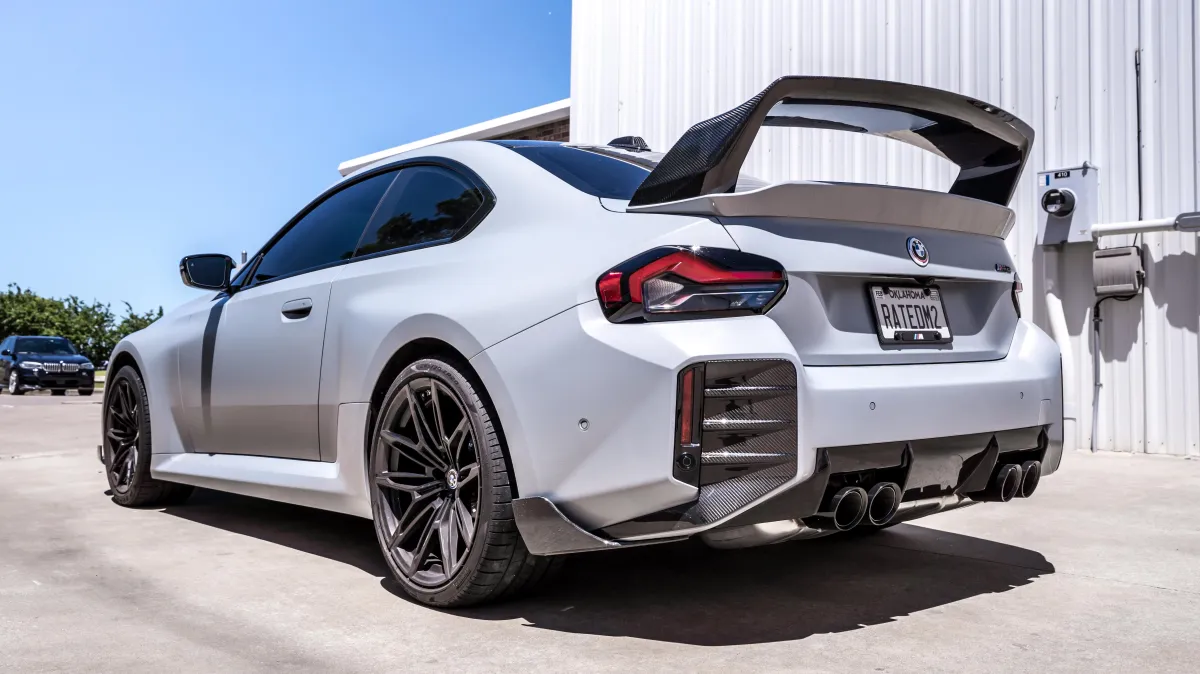
Turbocharging 101: How Turbos Work and Why They Boost Performance
The unmistakable whistle of a turbocharger spooling up, followed by the surge of power as boost builds, represents one of the most exciting developments in automotive engineering. What started as a technology for aircraft engines during World War I has evolved into one of the most effective methods for extracting maximum performance from internal combustion engines while maintaining efficiency and meeting increasingly strict emissions standards.
Turbocharging might seem like complex engineering magic, but the fundamental principle is elegantly simple: use exhaust gases that would otherwise be wasted to compress incoming air, allowing the engine to burn more fuel and produce significantly more power. This recycling of exhaust energy makes turbocharging one of the most efficient ways to increase engine output without dramatically increasing engine size, weight, or fuel consumption.
Modern turbocharging technology has reached remarkable levels of sophistication, with variable geometry turbines, electronically controlled wastegates, and advanced materials that allow turbos to operate reliably at extreme temperatures and pressures. Understanding how these systems work not only satisfies curiosity but also helps enthusiasts make informed decisions about modifications, maintenance, and performance upgrades.
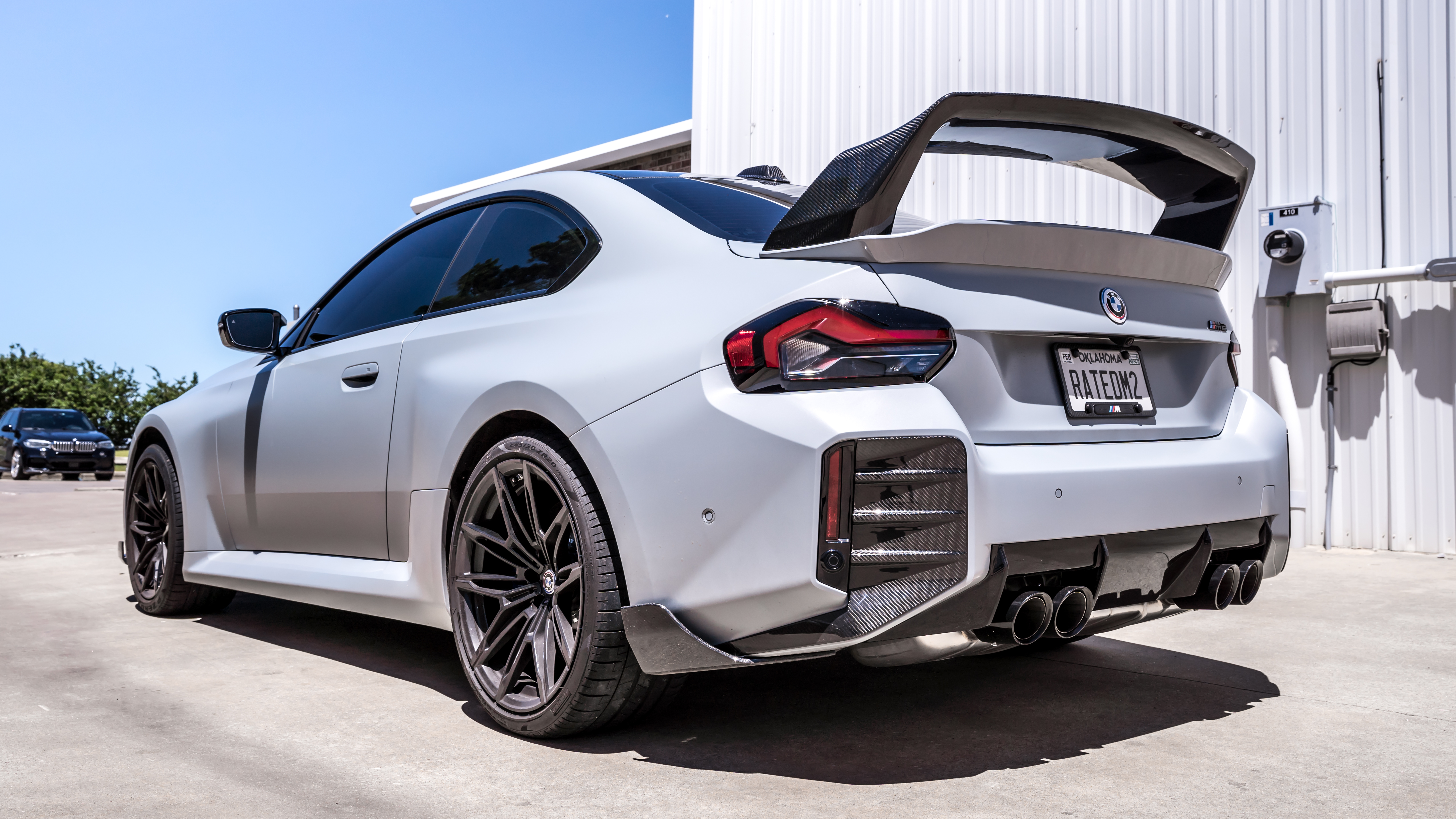
The Science Behind Turbocharging
At its core, a turbocharger is an air pump driven by exhaust gases. The basic principle exploits the fact that internal combustion engines are essentially air pumps themselves—the more air you can force into the cylinders, the more fuel you can burn, and the more power you can produce. Naturally aspirated engines rely on atmospheric pressure and the downward motion of pistons to draw air into the cylinders, but turbochargers actively compress incoming air to pack more oxygen into each cylinder.
The turbocharger consists of two main components connected by a common shaft: the turbine wheel and the compressor wheel. The turbine wheel sits in the exhaust stream, where hot, high-pressure exhaust gases cause it to spin at incredible speeds—often exceeding 100,000 RPM in high-performance applications. This spinning motion is transmitted through the shaft to the compressor wheel, which draws in ambient air and compresses it before forcing it into the engine's intake system.
The relationship between exhaust flow and boost pressure creates the characteristic power delivery of turbocharged engines. At low RPM, exhaust flow is relatively low, so the turbocharger spins slowly and produces minimal boost. As engine speed increases and exhaust flow intensifies, the turbocharger spins faster and produces more boost pressure. This creates the distinctive "surge" of power that turbocharged engines are famous for, often called "boost coming on" or "turbo spool."
Heat management represents one of the biggest challenges in turbocharger design. Exhaust gases can reach temperatures exceeding 1,800°F, and the compression process generates additional heat in the intake air. Hot air is less dense than cool air, which reduces the effectiveness of the turbocharger and can lead to detonation problems in the engine. This is why most turbocharged systems include intercoolers to cool the compressed air before it enters the engine.
The wastegate controls boost pressure by allowing some exhaust gases to bypass the turbine wheel when predetermined pressure levels are reached. Without this control mechanism, boost pressure would continue increasing with engine speed, potentially causing engine damage or component failure. Internal wastegates are built into the turbocharger housing, while external wastegates are separate components that offer more precise control and better flow characteristics for high-performance applications.
Bearing systems in turbochargers must operate reliably at extreme speeds and temperatures while maintaining precise tolerances. Traditional journal bearings use pressurized engine oil for lubrication and cooling, which is why proper oil maintenance is critical for turbocharger longevity. More advanced turbochargers use ball bearings or magnetic bearings that reduce friction and allow for quicker spool-up times and improved efficiency.
Advantages of Turbocharging Over Natural Aspiration
The primary advantage of turbocharging lies in its ability to increase power density—the amount of power produced per unit of engine displacement. A properly designed turbocharged engine can produce significantly more power than a naturally aspirated engine of the same size, often matching or exceeding the output of much larger engines while maintaining better fuel economy during light-load conditions.
Fuel efficiency represents one of turbocharging's most compelling benefits, particularly in modern automotive applications. During light-load driving conditions, such as highway cruising, a small turbocharged engine operates more efficiently than a larger naturally aspirated engine because it encounters less internal friction and pumping losses. The turbocharger only produces significant boost when needed, allowing the engine to operate efficiently during normal driving while providing substantial power when demanded.
Emissions reduction capabilities make turbocharging increasingly important as environmental regulations become more stringent. Smaller turbocharged engines typically produce lower CO2 emissions than larger naturally aspirated engines with equivalent power output. The improved combustion efficiency and reduced fuel consumption contribute to cleaner overall emissions, which is why many manufacturers have embraced turbocharging as part of their environmental strategy.
Altitude compensation represents another significant advantage of turbocharged engines. As altitude increases, atmospheric pressure decreases, which reduces the amount of air naturally aspirated engines can draw into their cylinders. This results in noticeable power loss at high altitudes. Turbocharged engines can maintain closer to sea-level power output at altitude because the turbocharger can increase boost pressure to compensate for the thinner air.
Torque characteristics of turbocharged engines often provide better driveability than naturally aspirated engines. Many turbocharged engines produce peak torque at relatively low RPM, creating strong acceleration from low speeds without requiring high engine speeds. This broad torque curve makes turbocharged engines feel responsive and effortless during everyday driving while still providing impressive high-RPM performance.
Weight and packaging advantages make turbocharging attractive for vehicle designers. A small turbocharged engine can produce the power of a much larger naturally aspirated engine while taking up less space and weighing significantly less. This weight reduction improves overall vehicle dynamics, fuel economy, and allows for better weight distribution in the chassis.

Common Turbocharger Configurations and Applications
Single turbocharger systems represent the most common and straightforward approach to forced induction. These systems use one turbocharger to pressurize all cylinders and offer excellent cost-effectiveness and simplicity. Single turbo setups work well for most applications and can be sized appropriately for different performance goals, from small turbos that provide quick spool and good driveability to large turbos that support extreme power levels at the expense of some low-end response.
Twin-turbo configurations come in several varieties, each with distinct advantages. Parallel twin-turbo systems use two identical turbochargers, with each typically feeding half the engine's cylinders. This approach can reduce turbo lag compared to a single large turbo while supporting high power levels. V-configuration engines often use this setup with one turbo per cylinder bank.
Sequential twin-turbo systems use two different-sized turbochargers that operate at different RPM ranges. A smaller turbo provides boost at low RPM for good response and driveability, while a larger turbo takes over at higher RPM to support maximum power output. The transition between turbos must be carefully calibrated to provide smooth power delivery, making these systems complex but potentially very effective.
Variable geometry turbochargers (VGT) use adjustable vanes in the turbine housing to optimize exhaust flow characteristics across different engine operating conditions. At low RPM, the vanes close to increase exhaust velocity and improve turbo response. At high RPM, the vanes open to reduce back pressure and support maximum power output. This technology provides many of the benefits of sequential twin-turbo systems in a single, more compact unit.
Electric turbochargers and hybrid systems represent the cutting edge of turbocharger technology. Electric assistance can eliminate turbo lag by spinning the compressor with an electric motor during low exhaust flow conditions. Some systems recover energy from the turbine during high-flow conditions to help power the vehicle's electrical systems. These advanced systems offer the potential for improved efficiency and response but add complexity and cost.
Application-specific turbocharger selection depends on the intended use and performance goals. Daily driver applications typically prioritize quick spool, broad torque curves, and reliability over peak power output. Track-focused builds might accept some low-end compromise in exchange for higher peak power and better high-RPM performance. Drag racing applications often use large turbos optimized for maximum power output, even if this creates significant turbo lag.
Turbo Lag and Modern Solutions
Turbo lag—the delay between pressing the throttle and feeling boost pressure build—has historically been one of the main criticisms of turbocharged engines. This phenomenon occurs because it takes time for exhaust flow to spin up the turbocharger and build boost pressure, particularly from low RPM or idle conditions. Understanding the causes of turbo lag and modern solutions helps explain why contemporary turbocharged engines feel much more responsive than earlier designs.
The primary cause of turbo lag is the rotational inertia of the turbocharger assembly. Heavier turbine and compressor wheels take more energy to accelerate from rest, creating longer delays before boost builds. Additionally, the volume of the intake and exhaust plumbing affects how quickly pressure changes can occur. Larger volumes take longer to pressurize, extending the time between throttle input and boost response.
Modern turbocharger design has dramatically reduced lag through several approaches. Smaller, lighter turbine and compressor wheels reduce rotational inertia, allowing faster spool-up times. Advanced materials like titanium and specialized alloys enable the construction of lighter components that can withstand the extreme operating conditions. Ball bearing centers reduce friction compared to traditional journal bearings, allowing turbos to spin up more quickly and coast down more slowly.
Twin-scroll turbocharger designs improve response by separating exhaust pulses from different cylinders. In a four-cylinder engine, cylinders 1 and 4 feed one scroll while cylinders 2 and 3 feed another. This separation prevents exhaust pulses from interfering with each other and maintains higher exhaust velocity to the turbine, improving low-RPM response while maintaining high-RPM performance.
Electronic wastegate control allows more precise boost management and can help reduce lag. Traditional pneumatic wastegates respond relatively slowly to pressure changes, but electronic systems can anticipate boost requirements and position the wastegate more quickly. This improved control can reduce the time needed to build boost and maintain more consistent pressure across different operating conditions.
Anti-lag systems, primarily used in motorsport applications, inject fuel into the exhaust stream to maintain turbine speed even when the throttle is closed. This keeps the turbo spinning at high RPM during gear changes or when off-throttle, virtually eliminating lag when the throttle is reapplied. However, these systems are hard on components and generally not suitable for street use due to their aggressive nature and potential impact on emissions and fuel economy.
Engine management strategies can minimize the perception of turbo lag through careful calibration of fuel delivery, ignition timing, and throttle response. Some systems use torque fill strategies that advance ignition timing during boost buildup to maintain power delivery, while others use electronic throttle control to modulate driver inputs for smoother power delivery.
Maintenance and Longevity Considerations
Proper maintenance is crucial for turbocharger longevity because these components operate under extreme conditions that can quickly lead to failure if neglected. Understanding the specific maintenance requirements of turbocharged engines helps ensure reliable operation and prevents costly repairs.
Oil quality and change intervals become critical with turbocharged engines because the turbocharger depends on engine oil for both lubrication and cooling. The extreme temperatures and high RPM operation of turbochargers place significant stress on the oil, breaking down its protective properties more quickly than in naturally aspirated engines. Using high-quality synthetic oil and maintaining shorter change intervals—often every 5,000 miles or less—is essential for turbo longevity.
Cool-down procedures help prevent oil coking and bearing damage in turbochargers. When a turbocharged engine is shut off immediately after hard driving, the turbocharger continues spinning while oil circulation stops, potentially causing oil to carbonize on hot bearing surfaces. Allowing turbocharged engines to idle for a minute or two after hard driving helps cool the turbocharger gradually and maintain oil circulation until temperatures drop to safe levels.
Heat soak management involves understanding how heat affects turbocharged systems and taking steps to minimize temperature-related problems. Proper heat shielding protects surrounding components from turbocharger heat, while adequate cooling system maintenance ensures the engine can manage the additional heat load created by forced induction. Some applications benefit from auxiliary cooling systems or heat management modifications.
Fuel quality becomes more important with turbocharged engines because the increased cylinder pressures and temperatures make these engines more sensitive to detonation. Using the recommended octane rating is crucial, and higher octane fuels may be beneficial for performance applications. Contaminated or low-quality fuel can cause detonation that damages pistons, rings, and other internal components.
Air filtration requires attention because turbochargers can amplify the effects of contaminated intake air. A clogged air filter not only reduces performance but can cause the turbocharger to work harder, potentially reducing its lifespan. High-flow air filters may improve performance but should be properly maintained to ensure adequate filtration. Oil-soaked filters from over-oiling can contaminate mass airflow sensors and cause drivability problems.
Warning signs of turbocharger problems include unusual noises, excessive smoke, loss of power, or oil consumption. Grinding or whining noises often indicate bearing problems, while blue smoke suggests oil is being burned in the combustion chambers. Black smoke typically indicates fuel system problems or boost leaks. Addressing these symptoms quickly can prevent complete turbocharger failure and potential engine damage.
Professional inspection and maintenance become more important with turbocharged engines because of their complexity and the potential for expensive failures. Regular inspections of boost hoses, intercooler systems, and wastegate operation can identify problems before they cause major damage. Many turbocharger problems can be prevented through proper maintenance and early intervention when symptoms appear.
Turbocharging represents one of the most effective ways to increase engine performance while maintaining efficiency and meeting modern environmental requirements. From the basic principles of exhaust-driven air compression to advanced variable geometry systems, turbocharger technology continues evolving to provide better performance, response, and reliability. Understanding how these systems work, their advantages and limitations, and proper maintenance requirements helps enthusiasts make informed decisions about turbocharged vehicles and modifications while ensuring long-term reliability and performance. Whether you're considering a turbocharged daily driver or planning a high-performance build, this knowledge forms the foundation for getting the most out of forced induction technology.